Организация трасс медных трубопроводов для систем кондиционирования
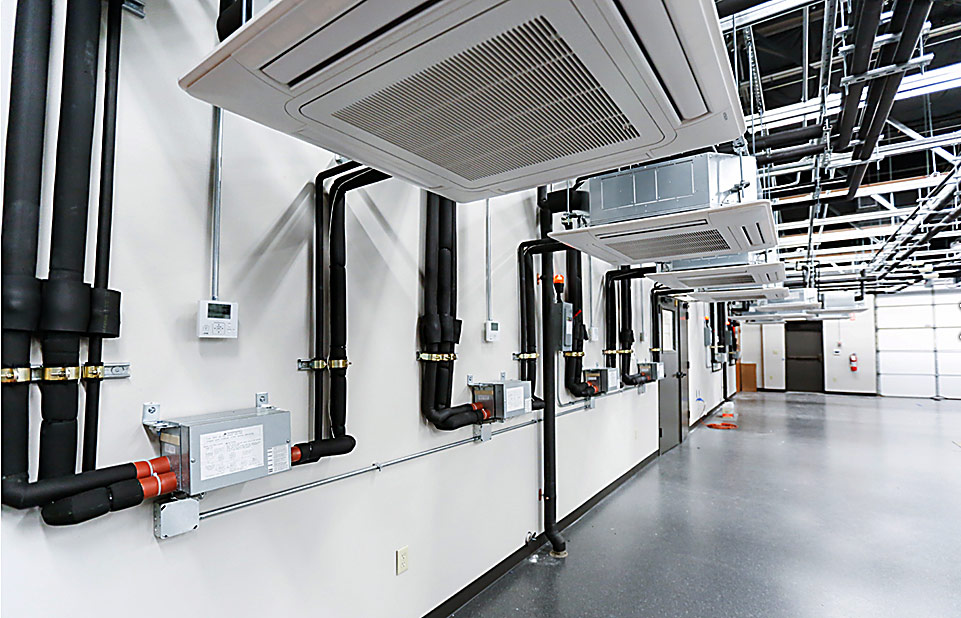
В процессе приёмо-сдаточных испытаний систем холодоснабжения регулярно приходится сталкиваться с инженерными ошибками, допущенными при проектировании и монтаже медных фреонопроводов для систем кондиционирования. Используя накопленный практический опыт, а также опираясь на требования нормативно-технической документации, мы постарались объединить основные технологические правила организации трасс медных коммуникаций в рамках данной статьи.
Речь пойдет именно об организации фреоновых магистралей, а не о механических аспектах монтажа медных трубопроводов. Будут рассмотрены вопросы пространственного размещения труб, их взаимного расположения, проблемы инженерного расчёта диаметра фреонопроводов, необходимость применения маслоподъёмных петель, температурных компенсаторов и других технических элементов. Мы обойдем стороной технологические нюансы монтажа конкретного трубопровода, методику выполнения соединений и иные детали. При этом будут затронуты вопросы более масштабного и комплексного подхода к устройству медных контуров, рассмотрены некоторые практические проблемные ситуации.Главным образом данный материал касается холодильных контуров систем кондиционирования, будь то традиционные сплит-системы, мультизональные VRF/VRV-системы кондиционирования или прецизионные кондиционеры для серверных помещений. При этом мы не затронем вопросы монтажа гидравлических трубопроводов в чиллерных системах и устройства относительно коротких фреоновых трубопроводов внутри холодильных агрегатов.
Нормативная документация по проектированию и монтажу медных трубопроводов
Среди нормативно-технической базы, касающейся монтажа медных трубопроводов, выделим следующие два основных стандарта:- СТО НОСТРОЙ 2.23.1–2011 «Монтаж и пусконаладка испарительных и компрессорно-конденсаторных блоков бытовых систем кондиционирования в зданиях и сооружениях»
- СП 40–108–2004 «Проектирование и монтаж внутренних систем водоснабжения и отопления зданий из медных труб».
Также мы использовали технические рекомендации производителей климатического оборудования, издаваемые ими в корпоративной документации.
Выбор диаметров медных трубопроводов
Выбор диаметра медных труб осуществляется на основе технических каталогов и специализированных программ расчета оборудования для кондиционирования воздуха. В бытовых сплит-системах диаметр труб выбирают по присоединительным патрубкам внутреннего и наружного блоков. В случае мультизональных VRF-систем правильнее всего использовать фирменные программы расчета производителя. В прецизионных кондиционерах для центров обработки данных используются заводские рекомендации поставщика. Однако при протяженной фреоновой трассе могут возникнуть нестандартные ситуации, не отражаемые в типовой технической документации.В общем случае для обеспечения гарантированного возврата компрессорного масла из контура в картер компрессора и приемлемых гидравлических потерь давления скорость потока в газовой магистрали должна быть не менее 4 метров в секунду для горизонтальных участков и не менее 6 метров в секунду для восходящих участков. Во избежание возникновения недопустимо высокого уровня шума максимально допустимая скорость газового потока ограничивается 15 метрами в секунду.
Скорость потока хладагента в жидкой фазе значительно ниже и ограничивается потенциальным гидравлическим ударом и разрушением запорно-регулирующей арматуры. Максимальная скорость жидкой фазы — не более 1,2 метра в секунду.На высоких подъемах при протяженных трассах внутренний диаметр жидкостной магистрали следует выбирать так, чтобы падение статического давления в ней и давление гидростатического столба жидкости (в случае восходящего трубопровода) не приводило к паровому пузырьковому вскипанию жидкости в конце магистрали.
В прецизионных системах кондиционирования, где длина трассы может достигать и превышать 50 метров, часто применяются вертикальные участки газовых магистралей заниженного диаметра, как правило, на один типоразмер (на 1/8").Также отметим, что зачастую расчетная эквивалентная длина трубопроводов превышает предельную, указанную производителем. В этом случае рекомендуется согласовать фактическую трассу с техническими специалистами производителя кондиционеров. Обычно выясняется, что превышение длины допустимо на величину вплоть до 50% максимальной длины трассы, указанной в технических каталогах. При этом производитель указывает необходимые коррективы в проект.
Маслоподъёмные петли
Маслоподъемные петли (или маслоподъёмники) устанавливаются на вертикальных участках фреоновой магистрали длиной 3 метра и более. При более высоких подъёмах газовой линии петли следует монтировать с интервалом каждые 3,5 метра по высоте. При этом в верхней точке вертикального участка устанавливается обратная маслоподъёмная петля для предотвращения обратного стекания масла.Однако и в этой области встречаются технические исключения. При согласовании нестандартной фреоновой трассы производитель климатического оборудования может как рекомендовать установку дополнительных маслоподъёмных элементов, так и разрешить отказ от некоторых из них. В частности, в условиях протяженной трассы с целью оптимизации общего гидравлического сопротивления контура часто рекомендуется отказ от обратной верхней петли. В другом реальном проекте из-за специфических условий эксплуатации на подъеме высотой около 3,5 метра инженерное решение предписывало установить две последовательные маслоподъемные петли.
Важно понимать, что маслоподъёмная петля является дополнительным гидравлическим сопротивлением в контуре и должна обязательно учитываться при расчете эквивалентной длины трассы и связанных с ней потерь давления.При изготовлении маслоподъёмной петли следует учитывать, что ее геометрические размеры должны быть минимально возможными. Общая протяженность петли не должна превышать 8 диаметров используемого медного трубопровода, чтобы не создавать избыточное сопротивление.
Крепление медных трубопроводов
Рис. 1. Схема крепления трубопроводов в одном из проектов,из которой крепление хомута непосредственно к трубе
неочевидно, что и стало предметом споров
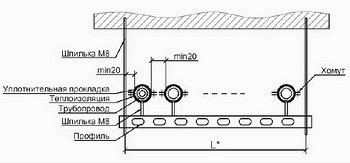
На самом деле для крепления труб должны использоваться металлические сантехнические хомуты с антивибрационными вставками, состоящие из двух полукорпусов, соединенных винтами и имеющие эластомерные уплотнительные элементы. Именно эти резиновые вставки обеспечивают необходимое гашение механических вибраций. Хомуты должны крепиться непосредственно к поверхности трубы, а не к теплоизоляции, должны соответствовать диаметру трубопровода и обеспечивать жесткую фиксацию трассы к строительным конструкциям (стене, потолку, металлоконструкциям).
Выбор шага крепления трубопроводов из твердых медных труб в общем случае рассчитывается по специальной инженерной методике, представленной в Приложении Г документа СП 40–108–2004. К данному аналитическому способу следует прибегать при использовании нестандартных трубопроводов или же в случае возникновения проектных разногласий. В повседневной практике инженеры чаще используют конкретные табличные рекомендации.ак, рекомендуемые значения расстояний между опорами медных трубопроводов приведены в таблице 1 (примечание: таблица отсутствует в исходном тексте). Расстояние между креплениями горизонтальных участков из полутвердых и мягких труб допустимо принимать меньше на 10 и 20% соответственно от значений для твердых труб. При необходимости более точного определения допустимого пролета между креплениями на горизонтальных трубопроводах следует использовать формульный расчет. На вертикальном стояке должно быть установлено как минимум одно крепление независимо от высоты этажа для обеспечения механической устойчивости системы.
Таблица 1. Расстояние между опорами медных трубопроводов
Диаметр трубы, мм | Пролет между опорами, м | |
Горизонтально | Вертикально | |
12 | 1,00 | 1,4 |
15 | 1,25 | 1,6 |
18 | 1,50 | 2,0 |
22 | 2,00 | 2,6 |
28 | 2,25 | 2,5 |
35 | 2,75 | 3,0 |
Отметим, что данные из табл. 1 приблизительно совпадают с графиком, изображенным на рис. 1 п. 3.5.1 СП 40–108–2004. Однако мы адаптировали данные этого норматива под используемые в системах кондиционирования трубопроводы относительно небольшого диаметра.
Компенсаторы температурного расширения
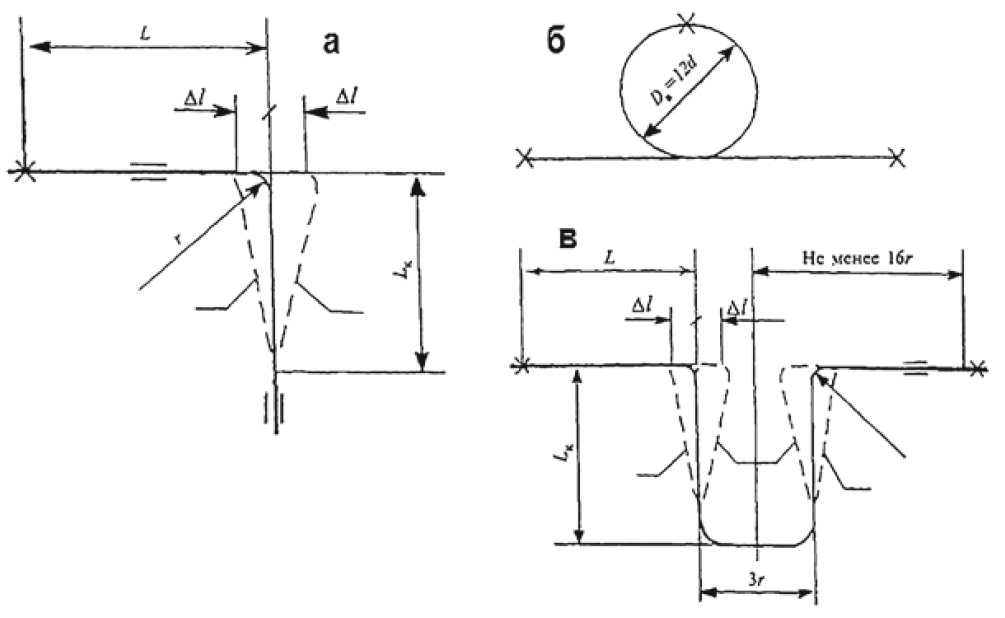
Рабочий хладагент в системах кондиционирования в общем случае имеет температуру в диапазоне от +5 до +75 °C (более точные значения зависят от конкретного участка холодильного контура и фазового состояния хладагента). Температура окружающей среды при этом может изменяться в широком диапазоне от –35 до +35 °C. Конкретные расчетные перепады температур принимаются в зависимости от места расположения рассматриваемого трубопровода (в помещении или на улице) и от его функционального назначения в холодильном контуре. Например, температура газообразного хладагента между компрессором и конденсатором находится в диапазоне от +50 до +75 °C, а температура жидкого хладагента между терморегулирующим вентилем (ТРВ) и испарителем — в диапазоне от +5 до +15 °C.
Традиционно в инженерной практике применяются П-образные и Г-образные компенсаторы. Аналитический расчёт компенсирующей способности П-образных и Г-образных элементов трубопроводов производится по формуле (см. схему на рисунке 2):

(Расчёт компенсирующей способности П-образных и Г-образных элементов трубопроводов)
гдеLк — вылет компенсатора, м;
∆L — линейная деформация участка трубопровода при изменении температуры воздуха при монтаже и эксплуатации, м;
А — коэффициент упругости медных труб, _А = 33_.
Линейная деформация определяется по формуле
p=. ∆L = α · L · ∆t, [2]
L — длина деформируемого участка трубопровода при температуре монтажа, м;
∆t — перепад температур между температурой трубопровода в различных режимах в процессе эксплуатации, °C;
α — коэффициент линейного расширения меди, равный 16,6·10–6 1/°C.
Для примера рассчитаем необходимое свободное расстояние Lк от подвижной опоры трубопровода d = 28 мм (0,028 м) до поворота, так называемый вылет Г-образного компенсатора при расстоянии до ближайшей неподвижной опоры L = 10 м. Участок трубы расположен внутри помещения (температура трубопровода при неработающем чиллере 25 °C) между холодильной машиной и выносным конденсатором (рабочая температура трубопровода 70 °C), то есть ∆t = 70–25 = 45 °C.
По формуле [2] находим:
p=. ∆L = α · L · ∆t = 16,6·10–6 · 10·45 = 0,0075 м.
Далее по формуле [1] находим:

(Расчет компенсирующей способности П-образных и Г-образных элементов трубопроводов)
Таким образом, конструктивного расстояния в 500 мм вполне достаточно для компенсирования температурных деформаций медного трубопровода. Ещё раз подчеркнем, что L — это расстояние до неподвижной опоры трубопровода, а Lк — расстояние до подвижной опоры трубопровода, определяющее размер компенсатора.При отсутствии естественных поворотов трассы и необходимости использования специального П-образного компенсатора получаем, что на каждые 10 метров прямого участка требуется полуметровый компенсатор. Если габаритные размеры технологического коридора или иные геометрические характеристики места прокладки трубопровода не позволяют устроить компенсатор с расчетным вылетом в 500 мм, компенсирующие элементы следует устанавливать с более частым шагом. При этом зависимость, как видно из математических формул, имеет квадратичный характер. При уменьшении расстояния между компенсаторами в 4 раза вылет компенсатора становится короче всего в 2 раза, что позволяет проектировать компактные компенсационные узлы даже в стесненных условиях.
Для быстрого определения вылета компенсатора удобно пользоваться табл. 2.Таблица 2. Вылет компенсатора Lк (мм) в зависимости от диаметра и удлинения трубопровода
Диаметр трубопровода, мм | Удлинение ΔL, мм | |||
5 | 10 | 15 | 20 | |
12 | 256 | 361 | 443 | 511 |
15 | 286 | 404 | 495 | 572 |
18 | 313 | 443 | 542 | 626 |
22 | 346 | 489 | 599 | 692 |
28 | 390 | 552 | 676 | 781 |
35 | 437 | 617 | 756 | 873 |
42 | 478 | 676 | 828 | 956 |
54 | 542 | 767 | 939 | 1 084 |
64 | 590 | 835 | 1 022 | 1 181 |
76 | 643 | 910 | 1 114 | 1 287 |
89 | 696 | 984 | 1 206 | 1 392 |
108 | 767 | 1 084 | 1 328 | 1 534 |
133 | 851 | 1 203 | 1 474 | 1 702 |
159 | 930 | 1 316 | 1 612 | 1 861 |
219 | 1 092 | 1 544 | 1 891 | 2 184 |
267 | 1 206 | 1 705 | 2 088 | 2 411 |
Наконец, отметим, что между двумя компенсаторами должна быть только одна неподвижная опора.
Потенциальные места, где могут потребоваться компенсаторы, безусловно, те, где наблюдается наибольший перепад температур между рабочим и нерабочим режимами работы кондиционера. Поскольку самый горячий хладагент протекает между компрессором и конденсатором, а самая низкая температура характерна для наружных участков зимой, то наиболее критичными являются наружные участки трубопроводов в чиллерных системах с выносными конденсаторами, а в прецизионных системах кондиционирования — при использовании внутренних шкафных кондиционеров и выносного конденсатора.
Подобная ситуация сложилась на одном из объектов, где выносные конденсаторы пришлось установить на раме в 8 метрах от здания. На таком расстоянии при перепаде температур, превышающем 100 °C, был всего один отвод и жесткое крепление трубопровода. Со временем в одном из креплений появился изгиб трубы, через полгода после ввода системы в эксплуатацию появилась утечка. Три системы, смонтированные параллельно друг другу, имели одинаковый дефект и потребовали экстренного ремонта с изменением конфигурации трассы, внедрением компенсаторов, повторной опрессовкой и перезаправкой контура.
Наконец, еще один фактор, который следует учитывать при расчете и проектировании компенсаторов температурного расширения, особенно П-образных, — значительное увеличение эквивалентной длины фреонового контура за счет дополнительной длины трубопровода и четырех отводов. Если общая длина трассы достигает критических значений (а если мы говорим о необходимости использования компенсаторов, длина трассы, очевидно, немаленькая), то согласовывать с производителем следует окончательную схему с указанием всех компенсаторов. В некоторых случаях совместными усилиями удается выработать наиболее оптимальное решение.
Общие рекомендации по монтажу трасс систем кондиционирования
Трассы систем кондиционирования следует прокладывать скрыто в бороздах, каналах и шахтах, лотках и на подвесах, при этом при скрытой прокладке должен быть обеспечен доступ к разъемным соединениям и арматуре путем устройства дверок и съемных щитов, на поверхности которых не должно быть острых выступов. Также при скрытой прокладке трубопроводов в местах расположения разборных соединений и запорной арматуры следует предусматривать сервисные лючки или съемные щиты.Вертикальные участки следует замоноличивать только в исключительных случаях. В основном их целесообразно размешать в каналах, нишах, бороздах, а также за декоративными панелями.
В любом случае скрытая прокладка медных трубопроводов должна производиться в защитном кожухе (например, в гофрированных полиэтиленовых трубах). Применение гофрированных труб из ПВХ не допускается из-за их неустойчивости к тепловому воздействию. До окончательной заделки мест прокладки трубопроводов необходимо выполнить исполнительную схему монтажа данного участка и провести гидравлические испытания фреонового контура.Открытая прокладка медных труб допускается в местах, исключающих их механическое повреждение при обычной эксплуатации помещений. Открытые участки можно закрывать декоративными коробами или специальными защитными профилями.
Прокладку трубопроводов через стены без гильз, надо сказать, наблюдать практически не приходится в современном строительстве. Тем не менее, напомним, что для прохода через строительные конструкции необходимо предусматривать гильзы (футляры), например из полиэтиленовых труб. Внутренний диаметр гильзы должен быть на 5–10 мм больше наружного диаметра прокладываемой трубы для обеспечения свободного температурного расширения. Зазор между трубой и футляром необходимо заделать мягким водонепроницаемым материалом, допускающим перемещение трубы вдоль продольной оси.При монтаже медных труб следует использовать специализированный инструмент — вальцовку для формирования конического расширения, трубогиб для создания плавных изгибов без изломов и потери проходного сечения, а также пресс-инструмент для правильного соединения фитингов.
Важно отметить, что соблюдение этих требований позволяет создавать долговечные и надежные фреоновые магистрали, а отступление от них нередко приводит к аварийным ситуациям, выходу из строя компрессорного оборудования и необходимости проведения сложных ремонтных работ.Советы опытных монтажников
Немало полезной информации о монтаже фреонопроводов можно получить от опытных монтажников систем кондиционирования. Особенно важно передавать данные сведения проектировщикам, поскольку одной из проблем проектной отрасли является ее оторванность от монтажа. Как следствие, в проекты закладываются трудно реализуемые на практике решения. Как говорится, бумага все стерпит. Начертить легко — выполнить сложно.Итак, одно из основных правил — обеспечить на проектном уровне удобную для монтажа высоту прокладки фреоновых трасс. Расстояние до потолка и до фальшпотолка рекомендуется выдерживать не менее 200 мм. При подвесе труб на шпильки наиболее комфортные длины последних — от 200 до 600 мм. Со шпильками меньшей длины трудно работать. Шпильки большей длины также неудобны в монтаже и могут раскачиваться.
При монтаже трубопроводов в лотке не следует подвешивать лоток к потолку ближе, чем на 200 мм. Более того, рекомендуется оставлять около 400 мм от лотка до потолка для комфортной пайки труб и формирования надлежащих соединений.Наружные трассы удобнее всего прокладывать именно в перфорированных лотках. Если позволяет разуклонка, то в лотках с крышкой. Если нет — трубы защищают иным способом, например, с помощью погодозащитного покрытия теплоизоляции.
Неизменная проблема многих объектов — отсутствие маркировки. Одно из самых распространенных замечаний при работе в сфере авторского или технического надзоров — промаркировать кабели и трубопроводы системы кондиционирования. Для удобства эксплуатации и последующего обслуживания системы рекомендуется маркировать кабели и трубы каждые 5 метров длины, а также до и после строительных конструкций. В маркировке следует использовать номер системы, тип трубопровода.При монтаже различных трубопроводов друг над другом на одной плоскости (стене) необходимо устанавливать ниже тот, у которого наиболее вероятно образование конденсата в процессе эксплуатации. В случае параллельного прокладывания друг над другом двух газовых линий различных систем, ниже должен быть установлен тот, в котором течет более тяжелый газ.
Заключение
При проектировании и монтаже крупных объектов с множеством систем кондиционирования и длинными трассами отдельное внимание следует уделять вопросам организации трасс фреонопроводов. Подобный подход разработки общей политики прокладки труб поможет сэкономить время как на этапе проектирования, так и на этапе монтажа. Кроме того, данный подход позволяет избежать массы ошибок, с которыми приходится встречаться в реальном строительстве: забытых компенсаторов температурного расширения или компенсаторов, которые не умещаются в коридоре из-за смежных инженерных систем, ошибочных схем крепления труб, неверных расчетов эквивалентной длины трубопровода.Как показал опыт реализации, учет этих советов и рекомендаций действительно дает положительный эффект на этапе устройства систем кондиционирования, заметно снижает число вопросов при монтаже и количество ситуаций, когда экстренно требуется найти решение сложной проблемы.
Тщательное планирование трасс фреонопроводов на стадии проектирования, следование нормативным требованиям и учет практических рекомендаций опытных монтажников позволяют создавать эффективные и долговечные системы кондиционирования, которые не только выполняют свои основные функции по созданию комфортного микроклимата, но и обеспечивают минимальные эксплуатационные затраты на протяжении всего жизненного цикла инженерной системы.